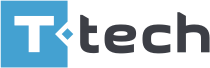
Человечество начало осваивать металл на заре становления цивилизации. Этот материал всегда ценился за прочность, долговечность и универсальность в применении, но его обработка была сопряжена с определенными трудностями. По этой причине металлический инструмент, орудия и предметы быта высоко ценились.
Однако с течением времени технологии металлообработки совершенствовалась, а настоящим прорывом стало появление станков для фрезерования.
Фрезерование решает ряд технологических задач, с которыми приходится сталкиваться в процессе изготовления механизмов и отдельных деталей. Заготовка обрабатывается с высокой точностью – допустимая погрешность не превышает десятые доли миллиметра. Минимизируется количество бракованных изделий, автоматизированный процесс практически исключает человеческий фактор.
Фрезерный станок имеет высокую производительность, он способен выполнять следующие операции:
Как и токарный станок, оборудование для фрезерования подходит для деталей из твердых материалов – прежде всего, металла. При этом используется режущий инструмент для выполнения технологических процедур, процесс автоматизирован за счет числового программного управления (ЧПУ).
Работы по металлообработке можно классифицировать по нескольким критериям. При выборе технического оснащения большое значение имеют планово-экономические показатели. Покупать производительные и высокоточные станки целесообразно только в том случае, если планируется большая загрузка участка. Для средне- и мелкосерийного производства подойдут консольные, настольные и универсальные модели.
По цикличности обработки возможна фрезеровка в прерывистом либо непрерывном цикле. Прерывистая технология предполагает применение вспомогательного обратного хода. Потребуется периодическое отключение станка, чтобы снять или закрепить деталь. Работа в непрерывном цикле синхронизирована с процессом снятия/установки.
По типу обрабатываемых поверхностей возможно вертикальное, горизонтальное или наклонное фрезерование. Применяется оснастка, имеющая заточку под определенным углом. Существуют комбинированные фрезы. Также мастер может задать вектор взаимного движения шпинделя станка и заготовки.
Фреза – это сменный инструмент, рабочим органом которого выступают зубья. Широко применяется твердосплавная оснастка с пластинами, которые не подлежат переточке. По конструкции фрезы подразделяются на следующие типы:
Зубчатый инструмент может располагать затылованными или остроконечными зубьями. От этого зависит сфера применения оснастки. Фрезы с остроконечными зубьями являются универсальными, в то время как затылованные аналоги по большей части подходят для фасонной обработки.
Технология фрезерования оказывает большое влияние на конечный результат. Оператор должен правильно подобрать сверло или фрезу, выбрать режим резания, скорость вращения шпинделя. Процесс фрезеровки состоит из следующих основных этапов:
Готовые детали могут подвергаться дальнейшей обработке, если этого требует проект. Например, возможна покраска или сварка фрезерованных металлоизделий, сборка сложного агрегата или механизма из отдельных деталей. Не исключено нанесение декоративных изображений способом лазерной гравировки.
Обрабатывать на фрезерных станках можно различные материалы, будь то алюминий, латунь, медь, бронза, сталь или композиты. Возможно изготовление изделий, различных по форме, размерам и функциональному назначению. Благодаря этому, фрезеровка стала широко востребованной технологией, применяемой в различных отраслях промышленности: