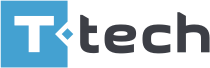
Глубокими считаются отверстия с отношением глубины к диаметру L/D > 5. Их обработка требует высокой точности и качества. Основные сложности: удаление стружки из длинного и узкого пространства, предотвращение вибраций и деформаций, эффективное охлаждения инструмента.
Выбор способа обработки зависит от материала детали, требуемой точности и допустимых погрешностей. Возможны отклонения по цилиндричности до 0,05 мм и шероховатости Ra до 1,6 мкм.
Торцевое фрезерование. При обработке этим методом возникают значительные ограничения. Глубина резания на один проход должна быть небольшой, что приводит к необходимости многопроходной обработки, увеличивает время и повышает риск погрешностей. Кроме того, эффективное охлаждение режущей кромки в условиях ограниченного доступа СОЖ затруднено.
Фрезерование с использованием специальных инструментов. Для улучшения процесса обработки глубоких отверстий могут быть задействованы концевые фрезы с удлиненным хвостовиком. Они позволяют увеличить глубину обработки за один проход, но при этом возрастает риск вибраций и изгиба инструмента.
Зенковки применяются для обработки конических или цилиндрических углублений в конце отверстия, часто после предварительного сверления. Позволяют получить более точную геометрию и произвести чистовую обработку.
Технология фрезерования глубоких отверстий имеет плюсы и минусы.
Преимущества:
Недостатки:
Как правило, фрезерование используется для получения глубоких отверстий реже, чем сверление или растачивание. Обычно его задействуют как вспомогательный метод для получения специальных профилей или финишных работ.
Выбор инструмента напрямую влияет на качество и производительность. Ключевым параметром является материал оснастки. Для глубоких отверстий обычно используются твердосплавные инструменты – по причине высокой износостойкости и прочности. В некоторых случаях могут применяться быстрорежущие стали. Нужно обращать внимание на следующие аспекты:
Режимы резания. Скорость (V), подача (f) и глубина (d) резания должны быть тщательно подобраны. Оптимальные режимы зависят от материала детали, инструмента и требуемого качества поверхности. Необходимо избегать чрезмерных нагрузок на оснастку.
СОЖ. Эффективное охлаждение и смазка критичны для предотвращения перегрева и улучшения качества металлообработки. Типы СОЖ варьируются от минеральных масел до синтетических жидкостей и эмульсий, выбор зависит от материала детали и инструмента.
Установка и крепление заготовки. Жесткая фиксация необходима для предотвращения вибраций, которые могут привести к снижению точности и повреждению инструмента. Методы крепления зависят от формы и размеров детали, и могут включать использование тисков, прихватов, центров и других специальных приспособлений.
Это неотъемлемая часть процесса, обеспечивающая соответствие полученных результатов заданным требованиям. С целью контроля качества применяют следующие методы оценки геометрических параметров:
Определение шероховатости поверхности Ra (среднее арифметическое отклонение профиля) выполняют с использованием профилометров или других методов. Требуемая шероховатость зависит от функционального назначения детали.