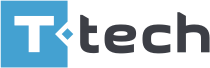
В сфере машиностроения и многих других производственных отраслей эффективность обработки металла на станках с ЧПУ является значимым фактором успеха. Рост производительности, снижение издержек и гарантированное высокое качество продукции – вот «три кита», на которых держится прибыльность любого предприятия, работающего с металлом.
Постоянное давление конкуренции заставляет компании искать новые способы оптимизации производственных процессов. Промпредприятия стремятся к максимальному использованию имеющегося оборудования и минимизации потерь.
Эта статья посвящена решению актуальной проблемы оптимизации обработки металла на станках с ЧПУ. В ней рассматриваются ключевые аспекты, влияющие на эффективность работы, такие как программирование, выбор режимов резания, наладка оборудования и контроль качества.
Мы уделим внимание практическим методам и стратегиям, направленным на повышение производительности и уменьшения времени обработки. Рассмотрим возможность снижения затрат на материалы и энергопотребление, а также повышение точности и качества готовых изделий.
Эффективная оптимизация начинается с глубокого понимания текущего состояния дел. Анализ включает в себя несколько ключевых этапов, позволяющих выявить «узкие места» (факторы, сдерживающие развитие) и определить направление для улучшений.
Анализ эффективности оборудования (ОEE). Такая метрика, как Overall Equipment Effectiveness или OEE позволяет оценить, насколько результативно используется станок с ЧПУ. OEE учитывает фактическое время работы, период простоев и процент брака, давая целостное представление о производительности оборудования. В процессе формирования метрики оценивается:
Временные исследования. Детальный хронометраж каждой операции в технологическом процессе позволяет точно определить время, затрачиваемое на ту или иную стадию обработки. Это дает возможность визуализировать операции, значительно замедляющие весь процесс. Для проведения таких исследований могут использоваться как ручные методы, так и специализированное программное обеспечение.
Анализ дефектов. Систематическая проверка бракованных изделий помогает определить причины возникновения дефектов и выявить операции, при которых они чаще всего возникают. В качестве методов проверки могут быть использованы диаграммы Парето и Исикавы («рыбьи кости» или Cause-and-Effect-Diagram). Они позволяют визуализировать вклад различных факторов в общий процент брака и определить приоритетные направления для улучшений.
Несмотря на компьютеризацию и автоматизацию производственных процессов, человеческий фактор продолжает оставаться немаловажным аспектом. Навыки и знания операторов играют ключевую роль в эффективности работы станка с ЧПУ, поэтому они нуждаются в оценке. В процессе аттестации персонала необходимо проверить:
По результатам проведенных тестов может быть выявлена необходимость в повышении квалификации кадров или замене неэффективных сотрудников. Это позволит не только повысить производительность процессов металлообработки, но и снизить количество брака и потенциально аварийных ситуаций на производстве.
Выбор и правильная установка инструмента – фундамент успешной обработки. Неподходящая оснастка может привести к браку, поломке и значительному снижению производительности. Ключевые моменты оптимизации:
Время, затрачиваемое на загрузку/выгрузку заготовок, напрямую влияет на общую производительность. Модернизация этого процесса – один из самых эффективных способов оптимизации.
Роботизированные модули и системы автоматической подачи заготовок значительно ускоряют процесс и минимизируют участие человека. Это не только повышает производительность, но и снижает риск человеческой ошибки.
Организация рабочего места. Эргономичное место оператора обеспечивает удобный доступ к оборудованию и материалам, сокращая время на вспомогательные операции. Правильная организация хранения инструмента и заготовок также способствует повышению эффективности.
Система охлаждения и смазки (СОЖ) играет важную роль в процессе металлообработки. Ее модернизация позволяет повысить качество обработки, увеличить срок службы инструмента и улучшить условия труда.
Применение СОЖ должно основываться на материале обрабатываемого металла и режиме резания. Неправильный выбор может привести к коррозии, снижению качества поверхности и преждевременному износу инструмента.
Эффективная система подачи СОЖ обеспечивает равномерное охлаждение и смазку резцов, минимизируя тепловое воздействие на обрабатываемую деталь и предотвращая образование нагара. Регулярный контроль состояния СОЖ и своевременная замена – залог бесперебойной работы оборудования.
Использование сенсоров. Датчики температуры, вибрации и силы резания позволяют отслеживать состояние процесса в режиме реального времени. Эти данные помогают выявить потенциальные проблемы и предотвратить аварийные ситуации.
Система сбора и анализа данных. Необходимо наработать базу, позволяющую выявлять тенденции производства. Она поможет прогнозировать возможные отклонения и оптимизировать параметры обработки на основе полученных результатов.