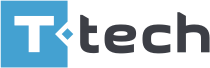
Надёжность всех узлов механизма напрямую зависит от качества металлообработки каждой детали. В машиностроении качество изделия определяется тем, насколько оно соответствует чертежу и техническим условиям. Во время металлообработки заготовку подвергают тепловому, механическому и химическому воздействию. Благодаря чему ей придают заданные параметры. После обработки каждая деталь проходит контроль качества и, при необходимости, возвращается на ручную доработку.
Что означает точность металлообработки:
Высокая точность металлообработки требует использования дорогого современного оборудования, качественных материалов и высокой квалификации мастеров. Всё это повышает затраты на производство и снижает скорость изготовления деталей, что не всегда бывает оправдано. В свою очередь низкая точность обработки, ухудшает качество изделий, увеличивает сложность сборки механизма, так как требует дополнительной подгонки на месте, а также может стать причиной аварии и несчастного случая.
Для разных задач необходимо разное качество деталей. Например, элементы медтехники или измерительных приборов должны иметь более точную обработку, чем детали сельскохозяйственных машин и инструментов. Именно поэтому в производстве используется разделение на классы точности. Класс точности показывает диапазон допустимых отклонений от заданных параметров. Современный ГОСТ устанавливает 11 классов точности, от 1 — самого высокого до 11 — самого низкого. Большее применение в промышленности получили первые пять классов.
Как происходит разделение:
Благодаря такому разделению удалось оптимизировать процесс изготовления деталей. Нет смысла переплачивать за слишком сложное производство, если к качеству изделия предъявляются более низкие требования. Когда точность металлообработки определяется конкретными цифрами, появляются чёткие критерии, которые можно измерить.
При производстве больших партий машин применяются идентичные друг другу детали механизмов. Это упрощает процесс изготовления изделий, уменьшает их стоимость и сокращает время сборки. Каждый элемент должен собираться в общий узел без предварительной подгонки и заменять другой в случае его поломки. Такой принцип изготовления деталей и называют взаимозаменяемостью.
Чтобы разные элементы могли соединяться друг с другом, они должны иметь стандартизированные размеры. Сопряжение — это способность деталей объединяться в единую пару, без дополнительной подгонки. Именно с помощью точной металлообработки удается создать качественные взаимозаменяемые и сопряжённые изделия, которые создают надёжные узлы и механизмы.